In the world of interior design, tin plate ceiling tiles are making a remarkable comeback, powered by both nostalgia for vintage aesthetics and the undeniable durability these tiles offer. As we delve into the story of manufacturing tin plate ceiling tiles, one can appreciate the blend of artistry and engineering that defines this industry.
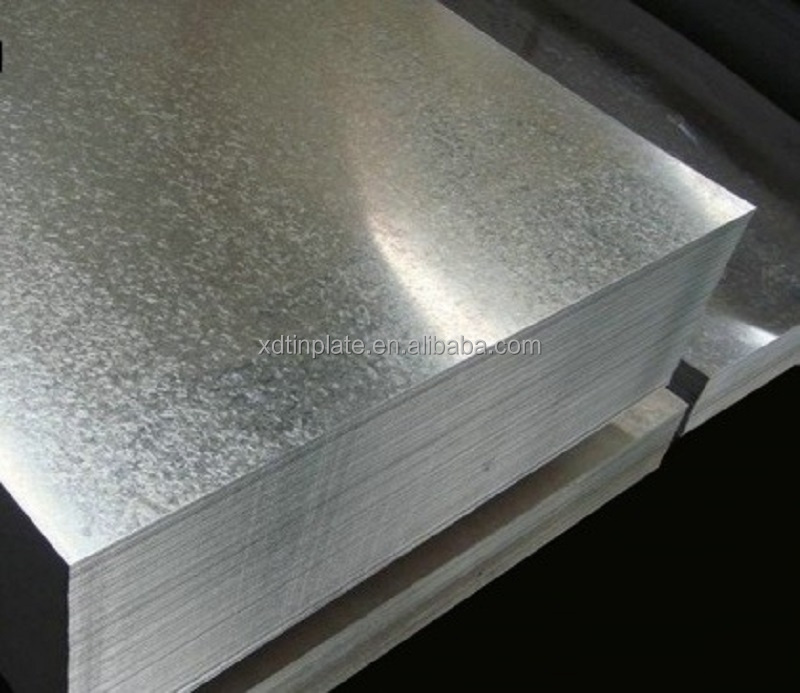
A journey through a tin plate ceiling tiles factory is like stepping into a realm where tradition meets technology. These factories are bustling hubs of activity, each stage meticulously planned to create tiles that combine both function and beauty. From the inception of a design to the dispatch of a finished product, every step is executed with a precision that mirrors the artistry of the tiles themselves.
The production process begins with the careful selection of raw materials. Factories source high-quality tin to ensure durability and a superior finish. This selection process is more than just choosing a metal; it's about understanding the characteristics that will lead to a product that is both lasting and aesthetically pleasing. Expertise in material science plays a critical role here, as the right choice of tin directly impacts the tile's effectiveness in resisting corrosion and maintaining its luster over time.
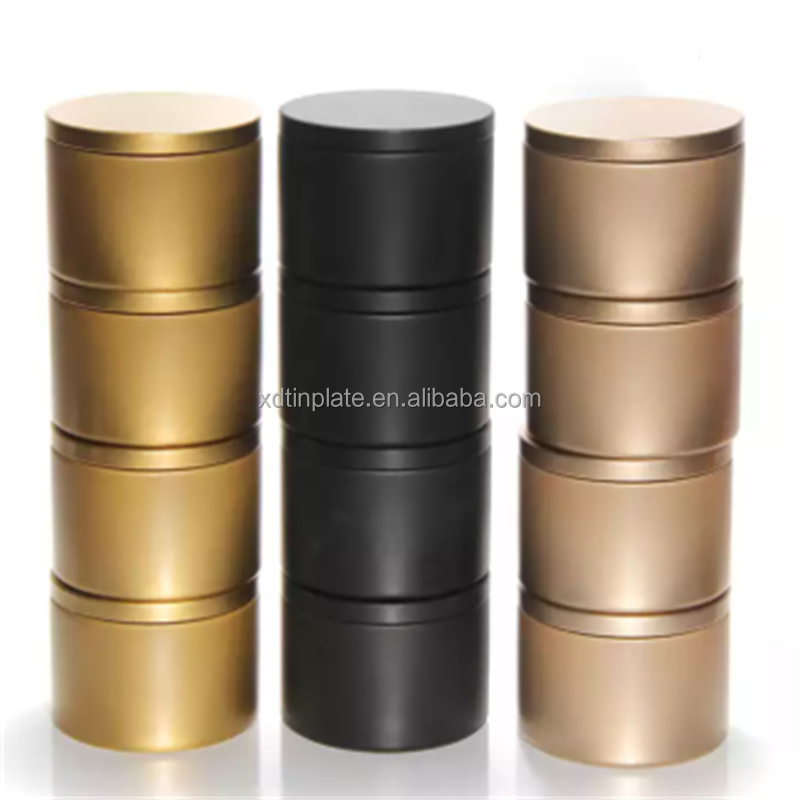
Next is the design phase, where creativity meets expertise. Skilled craftsmen and women use state-of-the-art technology to transform ideas into tangible patterns. Computer-aided design software enables these artisans to experiment with intricate patterns and textures, drawing inspiration from both classical motifs and modern designs. This phase is crucial, as it sets the stage for tiles that not only fulfill decorative aspirations but also adhere to high standards of quality and precision engineering.
The manufacturing process is a testament to technological advancement complementing human skill.
Modern tin plate ceiling tile factories utilize advanced press machines to emboss designs onto the tin sheets. This process requires authoritative knowledge of machinery and control parameters to ensure that each tile's embossed design meets the intended specifications. The precise alignment and pressure management during embossing are pivotal, demanding both expertise and experience from the operators.
tin plate ceiling tiles factory
After embossing, the tiles undergo a rigorous quality assurance phase. Here, each tile is inspected for uniformity, structural integrity, and adherence to design specifications. Factories often employ both automated and manual inspection methods, demonstrating a commitment to trustworthiness and reliability. Tiles that pass this stage are ones that will grace ceilings with their beauty for decades to come.
Finally, the finished tiles are treated with protective coatings. This crucial step enhances durability and helps maintain the aesthetic appeal, protecting against elements like moisture and air pollutants. This treatment is another layer of assurance that the product will serve its purpose without compromise.
In a market where credibility is paramount, a factory that specializes in creating tin plate ceiling tiles must uphold principles of transparency and trustworthiness. This involves not only adhering to high production standards but also engaging with clients and partners with integrity and honesty.
For any interior designer, architect, or homeowner considering tin plate ceiling tiles, understanding this comprehensive process provides an assurance of quality and craftsmanship. Whether restoring a historic property or designing a new contemporary space, these tiles offer a timeless elegance backed by an industry that respects both tradition and innovation.
In sum, a tin plate ceiling tiles factory exemplifies a confluence of experience, expertise, authority, and trust, resulting in products that stand as a testament to both aesthetic beauty and long-lasting functionality.