Roof racks specially designed for sheet materials have revolutionized the way factories manage storage and transportation. These innovative solutions cater specifically to industries dealing with large, flat materials, providing unmatched convenience, safety, and efficiency. Understanding the complexities involved in optimizing these systems for factory use requires expertise, authority, and a deep understanding of the needs and challenges faced by such operations.
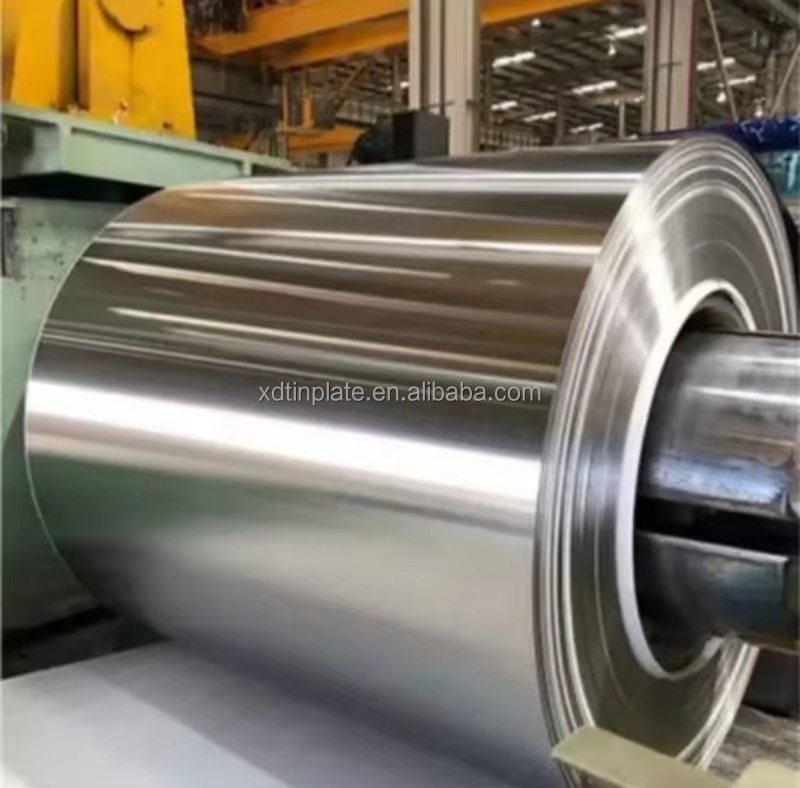
In any factory setting, the logistics of moving and storing sheet materials like steel, aluminum, or composite panels can significantly impact productivity and costs. Traditional storage solutions and transport methods often come with limitations, leading to inefficiencies. This is where roof racks engineered for sheet materials stand out, offering factories a tailor-made solution that boosts both performance and safety.
Experience in the field indicates that the incorporation of sheet material roof racks contributes to a more organized and streamlined workflow, which is crucial for maintaining consistent output rates. By elevating materials above the workspace, these racks make better use of vertical spaces, which is often underutilized in factory layouts. This maximization of space not only enhances the storage capacity without the need for floor expansion but also facilitates quicker access and retrieval times.
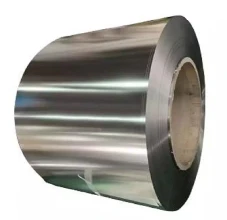
From the perspective of expertise, it is vital to understand that these roof racks are not merely generic shelving solutions. They are often custom-built to accommodate the specific dimensions and weights of the materials they support. High-grade materials such as galvanized steel and heavy-duty aluminum are commonly used in construction, ensuring durability and longevity even under constant use or adverse conditions. Furthermore, understanding the load dynamics and material properties is critical in designing these racks to prevent accidents and ensure the safety of workers and materials alike.
roof rack for sheet materials factories
Authority in this area stems from the knowledge of industry standards and safety regulations that govern the use of such storage solutions. Compliance with guidelines issued by bodies such as the Occupational Safety and Health Administration (OSHA) and the International Organization for Standardization (ISO) ensures that factory operations remain within legal and safety parameters, which is crucial for avoiding costly fines and ensuring employee well-being. Factories utilizing roof racks that adhere to these standards can reassure both employees and clients of their commitment to excellence and safety.
Trustworthiness is perhaps the most essential aspect when a factory decides on implementing or upgrading to roof racks for sheet materials. Selecting a reputable supplier with a proven track record in manufacturing and installing these systems is crucial. Due diligence steps, such as reviewing client testimonials, case studies, and asking for references, can provide valuable insights into the dependability of the product and the expertise of the supplier. Moreover, offering after-sale support and maintenance services is a hallmark of a reliable provider, ensuring any issues can be promptly addressed to maintain operational efficiency.
In conclusion, roof racks optimized for sheet materials are indispensable in modern factory settings, providing tangible benefits through improved space management and operational efficiency. Expertise in selecting and customizing these solutions facilitates their seamless integration into existing workflows, while authority in adhering to safety standards ensures a secure work environment. Trustworthy suppliers play a pivotal role in delivering high-quality and dependable products, cementing the importance of strong partnerships in achieving optimal factory performance. These roof racks are not just an addition to the infrastructure but a strategic investment towards a more efficient, organized, and safe operational framework.