Understanding the relative roughness of galvanized iron surfaces is crucial for industries that rely on piping systems, roofing, and other construction applications. This article delves into the concept of relative roughness, its implications for galvanized iron factory applications, and why understanding this parameter can enhance efficiency and reliability in industrial operations.
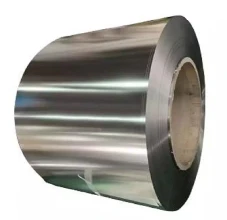
Relative roughness refers to the ratio of the height of surface irregularities to the diameter of the pipe or the thickness of the material it’s applied to. For galvanized iron, which is commonly used due to its corrosion resistance and durability, mastering this concept is pivotal not only for manufacturers but also for end-users who prioritize product longevity and performance.
One of the primary reasons relative roughness is significant is its impact on fluid flow within pipes. Smooth surfaces allow fluids to move with minimal friction loss, which can significantly affect energy consumption and operational costs in factories. A galvanized iron surface with higher roughness could lead to increased turbulence, reducing system efficiency. By optimizing the relative roughness of galvanized iron pipes, factories can enhance their system performance and reduce energy costs over time.
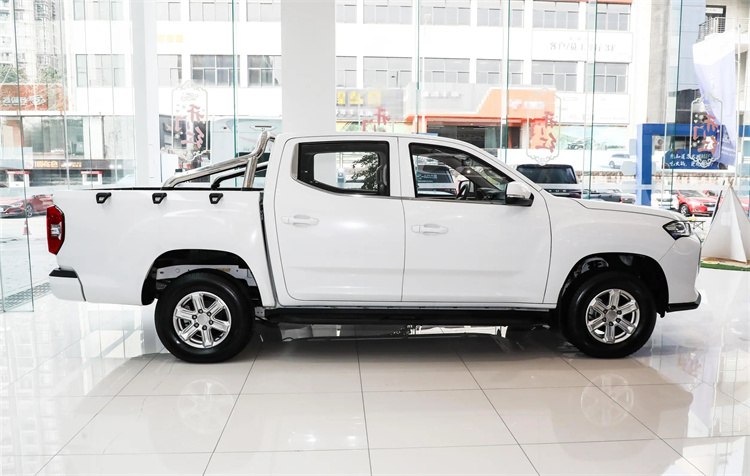
Professionals in the construction and manufacturing industries often seek expertise in selecting materials based on relative roughness to achieve desired outcomes.
Here’s why expertise in relative roughness evaluation is paramount
1. Material Longevity and Reliability Understanding and selecting the correct surface roughness ensures minimal degradation over time. Lower relative roughness typically indicates not just better flow characteristics, but also reduced wear and accumulation of debris, leading to prolonged service life of pipes and construction materials.
2. Installation and Maintenance Manufacturers with deep expertise in material science ensure that galvanized iron products undergo rigorous testing to maintain optimal roughness levels. During installation, understanding roughness can also assist in precise fitting and sealing, which helps in maintaining system integrity and reducing maintenance interruptions.
relative roughness of galvanized iron factory
3. Cost-Effectiveness Utilizing materials with optimal roughness can lead to reduced operational costs. Factories benefit from decreased energy consumption due to optimized flow, and the need for replacements and repairs diminishes, impacting the bottom line positively.
From an expertise standpoint, engineers and technical consultants possess the authority to guide factories and construction firms in selecting and testing materials that align with their specific needs. Their authoritative insights ensure that the selected materials not only meet but exceed industry standards, offering a layer of trustworthiness to stakeholders and clients.
Several authoritative sources in the field, such as ASME and ASTM standards, provide detailed guidelines on measuring and interpreting relative roughness, adding further credibility to insights backed by such standards. Consulting these resources ensures that industrial applications not only comply with regulations but also achieve high levels of efficiency and safety.
Trustworthiness, in this context, also entails providing factual and transparent data about the materials used. By leveraging advanced surface analysis technologies, manufacturers of galvanized iron ensure their products uphold the highest quality, thus instilling confidence in their clients.
In conclusion, for galvanized iron factories, understanding relative roughness is not merely a technical specification but a pivotal factor that influences the overall efficiency, cost-effectiveness, and reliability of their operations. By combining real-world experience with technical expertise and an authoritative approach, stakeholders can harness the full potential of galvanized iron in various industrial applications. This knowledge not only drives better decision-making but also fortifies the trust between manufacturers and their clients, setting a benchmark for excellence and reliability in the industry.