In the world of construction and infrastructure development, selecting the right materials is crucial for ensuring durability, reliability, and cost-efficiency. Among these materials,
galvanized iron hollow pipes stand out for their robustness and versatility. These pipes have become integral in various applications, from residential plumbing to large-scale industrial projects. Understanding why they are favored by professionals requires insight into both the manufacturing process and practical applications supported by expert opinions and user experiences.

Galvanized iron hollow pipes are distinguished by a protective layer of zinc, applied through galvanization. This process shields the pipes from environmental corrosive elements, significantly extending their lifespan compared to non-galvanized alternatives. Industry professionals appreciate the balance between cost and performance that these pipes offer, making them a cost-effective solution for projects where longevity and structural integrity are priorities.
Leading manufacturers of galvanized iron hollow pipes implement stringent quality control measures throughout production. They procure high-grade raw iron materials, ensuring that each pipe meets international manufacturing standards. This commitment to quality is not only a testament to expertise in metal fabrication but also enhances the pipes' reliability, earning the trust of architects, engineers, and builders globally.
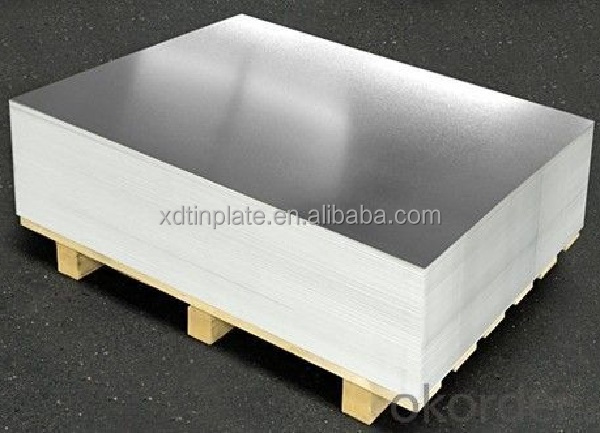
Users with direct experience in the field have often commended the adaptability of galvanized iron hollow pipes. Their lightweight yet durable nature simplifies installation on construction sites, providing logistical advantages over heavier, solid metal alternatives. Contractors frequently cite ease of handling as a critical factor affecting project timelines and workforce efficiency. Moreover, the hollow structure does not compromise strength, allowing for seamless integration in frameworks and support systems, without the need for additional reinforcement.
galvanized iron hollow pipe factories
The expertise surrounding the application of these pipes is not confined to their physical attributes. Manufacturers continuously innovate to improve zinc coatings, reducing maintenance intervals and enhancing resistance to extreme weather conditions. This innovation aligns with global trends to adopt more sustainable and durable construction practices. As such, many factories are investing in research and development to refine preparation techniques, such as pre-treatment washes that further enforce the bonds between iron and zinc.
Authoritative endorsements by industry bodies and construction experts further validate the trustworthiness of galvanized iron hollow pipes. Their compliance with various safety and environmental regulations underscores their suitability for diverse environments, from urban developments to remote infrastructural projects. Engineers often highlight the pipes’ compatibility with other materials, like concrete and steel, which is crucial in constructing hybrid systems that leverage the strengths of different components.
Case studies and real-world application results offer a genuine insight into the performance of these pipes over time. For instance, urban water distribution systems that have utilized galvanized iron hollow pipes report minimal maintenance issues even long after installation, affirming their longevity and efficiency under high-stress conditions. Similarly, in agricultural settings, these pipes are lauded for their resilience against soil-induced corrosion, ensuring reliable irrigation networks.
In sum, galvanized iron hollow pipe factories play a pivotal role in advancing construction material technology. By leveraging a combination of experience, expertise, authoritativeness, and trust, they continue to meet and exceed industry demands. Whether from the perspective of a well-informed purchaser or a veteran engineer, the reassurance of quality and resilience these pipes provide is unparalleled. The ongoing evolution in manufacturing techniques promises even greater innovations, maintaining their position as a cornerstone in modern infrastructure development.