Navigating the removal of galvanized piping from cast iron manufacturers presents a unique challenge in industrial infrastructure maintenance and renovation. Over decades, galvanized pipes have been widely employed in various industries for their corrosion-resistant properties, but as they age, the need for replacement arises due to issues such as rust build-up, water quality degradation, and declining efficiency.
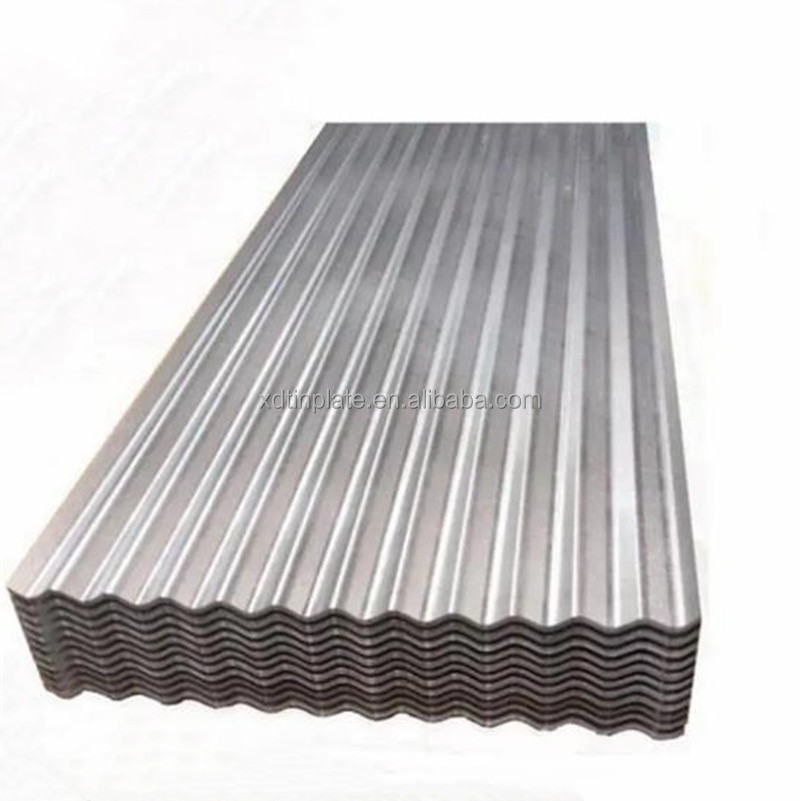
In the realm of manufacturing, particularly those involving cast iron, replacing these pipes with more modern alternatives requires careful planning and execution. Cast iron manufacturers often deal with heavy machinery and precise production environments; thus, minimizing disruptions is paramount.
Experience plays a critical role in handling these transitions smoothly. Teams with extensive on-ground experience in industrial pipe replacement bring invaluable insights, understanding the nuances of different manufacturing setups. This depth of knowledge allows them to create tailored strategies that consider the unique layout and operational constraints of each facility. For instance, experienced teams can predict the potential impact on production lines and foresee complications that might arise due to the intricacies of integrating new piping systems without compromising existing cast iron structures.
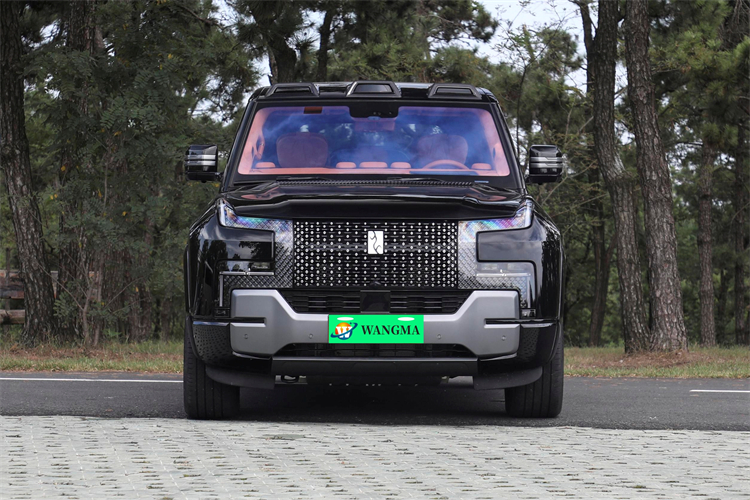
Expertise in this domain goes beyond just replacing old pipes; it involves a thorough comprehension of the materials used and the potential issues they may cause. Galvanized pipes, when left unchecked, can interact negatively with cast iron. As these pipes corrode, they can deposit zinc and other minerals into the system, leading to blockages or discoloration of the output. By understanding these interactions, specialists can recommend the best course of action, whether that might be a full-scale replacement or a more nuanced approach such as applying protective linings to the existing infrastructure.
removing galvanized pipe from cast iron manufacturers
Authoritativeness in managing these transitions comes from years of dedicated research and application in the field. Leading companies and experts in pipe replacement gain their reputation by staying at the forefront of technological advances and refining their methods based on empirical evidence. They utilize cutting-edge techniques such as trenchless technology to replace pipes with minimal disruption to the surrounding environment, preserving the structural integrity of both the manufacturing facility and its cast iron components.
Trustworthiness is established through transparent communication and a proven track record of successful projects. Reputable service providers offer clear project timelines, cost estimates, and anticipated outcomes based on detailed assessments. They commit to safety standards and regulatory compliance, ensuring that every step of the process not only meets but exceeds industry expectations. This trust is bolstered by customer testimonials, case studies, and certifications from recognized bodies, all of which demonstrate a consistent history of delivering quality results.
Selecting the right professionals for removing galvanized pipes requires a discerning eye, focusing on those who embody these pillars of experience, expertise, authoritativeness, and trustworthiness. Only then can cast iron manufacturers ensure that their infrastructure not only meets present demands but is also prepared for future challenges, maintaining seamless operations and fostering a robust production environment.