Hollow roof sheets have become an essential choice for modern construction, providing an excellent combination of durability, cost-effectiveness, and aesthetic appeal. These sheets are especially favored for residential homes, commercial structures, and industrial facilities. To delve into this topic, it's crucial to explore the production prowess of hollow roof sheet factories, tapping into the nuances of their operations and the quality of their products to understand their widespread efficacy.

A notable feature of hollow roof sheets is their lightweight nature, which does not compromise on strength. This balance is achieved through precise manufacturing processes honed by expert engineers and technicians in these factories. They utilize high-grade raw materials such as polycarbonate and PVC compounds, recognized for their resilience and longevity. The meticulous blending and testing of these materials affirm the product's capacity to withstand extreme weather conditions, UV radiation, and mechanical impacts, ensuring a long service life.
Factories specializing in these designs employ state-of-the-art machinery, which is central to guaranteeing uniformity and quality. Extrusion techniques, refined over years of research and development, play a pivotal role in shaping these sheets. Skilled operators monitor the machinery to adjust temperatures, pressures, and speeds to attain the desired thickness and hollow core structure. This not only reinforces the sheet but also contributes to enhanced thermal insulation, proving advantageous in various climate zones.
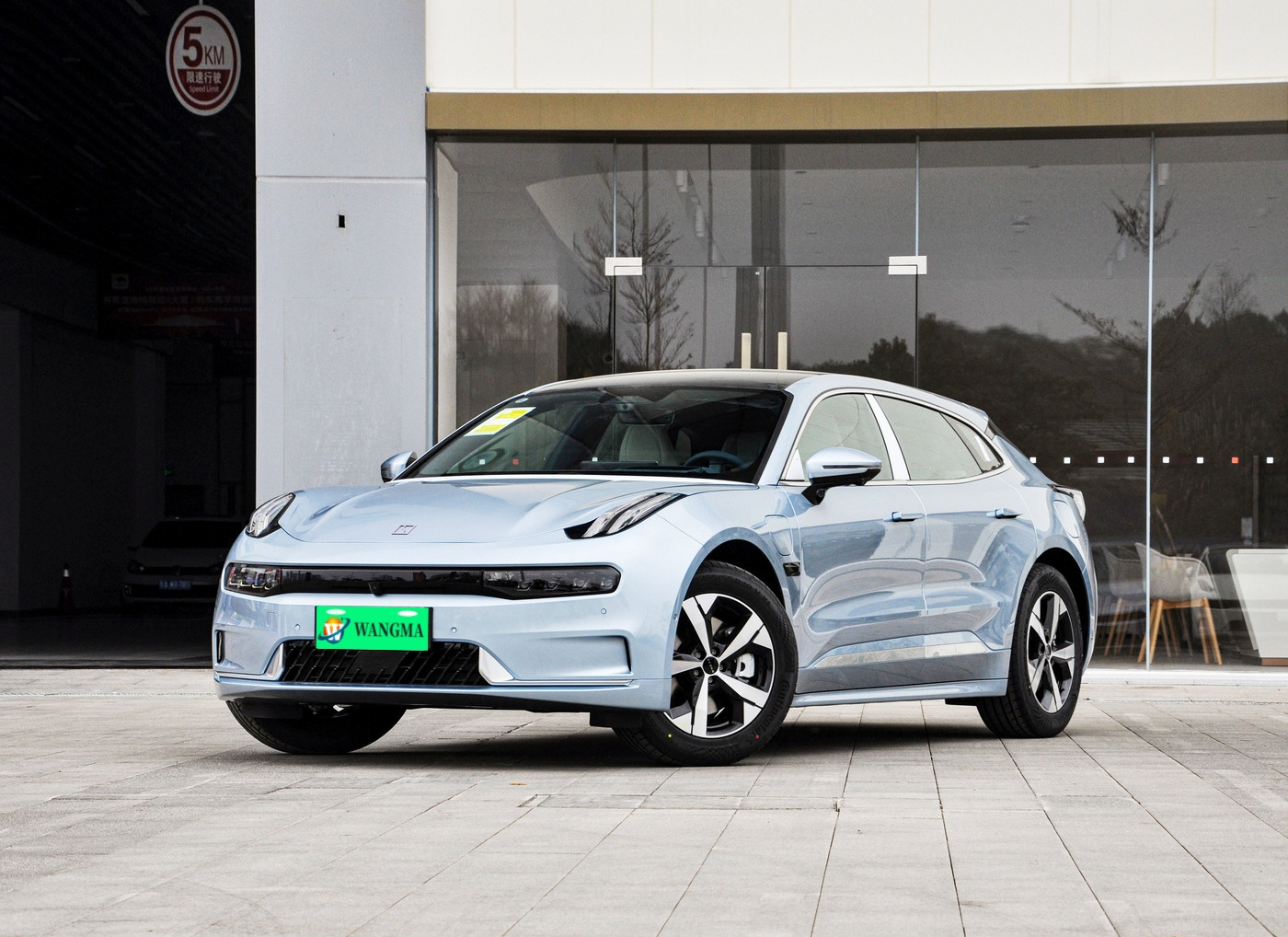
Product development in hollow roof sheet factories is defined by continuous innovation and adherence to international quality standards. Experts in these facilities conduct comprehensive research trials to explore new resin combinations and structural modifications, always aiming to augment performance metrics like fire resistance, sound absorption, and energy efficiency. Their commitment to excellence is further evidenced by the certifications they hold, which often align with global benchmarks such as ISO standards, further cementing their credibility in the marketplace.
hollow roof sheet factories
The user-centered approach taken by these manufacturers extends into customizable options that cater to design flexibility. Architects and builders appreciate the ability to select from a spectrum of colors, finishes, and profiles that suit their specific project needs, allowing for creative freedom without compromising structural integrity. The customizable aspects also ensure that these panels seamlessly integrate into diverse architectural styles.
Sustainability is another cornerstone of reputed hollow roof sheet factories, contributing directly to their authoritative standing in the industry. Many factories have implemented environmentally friendly practices in their production lines, such as recycling off-cuts and minimizing emissions. Additionally, the long lifespan and energy-efficient nature of the sheets align with green building principles, offering environmentally responsible solutions to contemporary construction challenges.
Customer trust is solidified through comprehensive service offerings that encompass pre-sale consultations, installation guidance, and after-sale support. Experienced teams provide valuable insights into product selection and optimal usage, fostering informed decision-making. This holistic approach underscores the trustworthiness of these manufacturers, reassuring clients of the product's reliability from purchase through to installation.
In essence, hollow roof sheet factories symbolize a blend of experience, expertise, authority, and trust. They are not merely production hubs but are pivotal in progressing construction material technologies. Their dedication to quality, sustainability, and customer satisfaction differentiates them in an increasingly competitive market, reflecting why hollow roof sheets are a preferred choice for many modern-day applications.