As an industrial sector, tin mill black plate factories play a significant role in producing essential materials used in the manufacturing of a wide array of tin-coated products. From high-end packaging solutions to durable parts in automotive industries, understanding the intricacies of this particular segment can empower stakeholders to harness its full potential for their businesses.
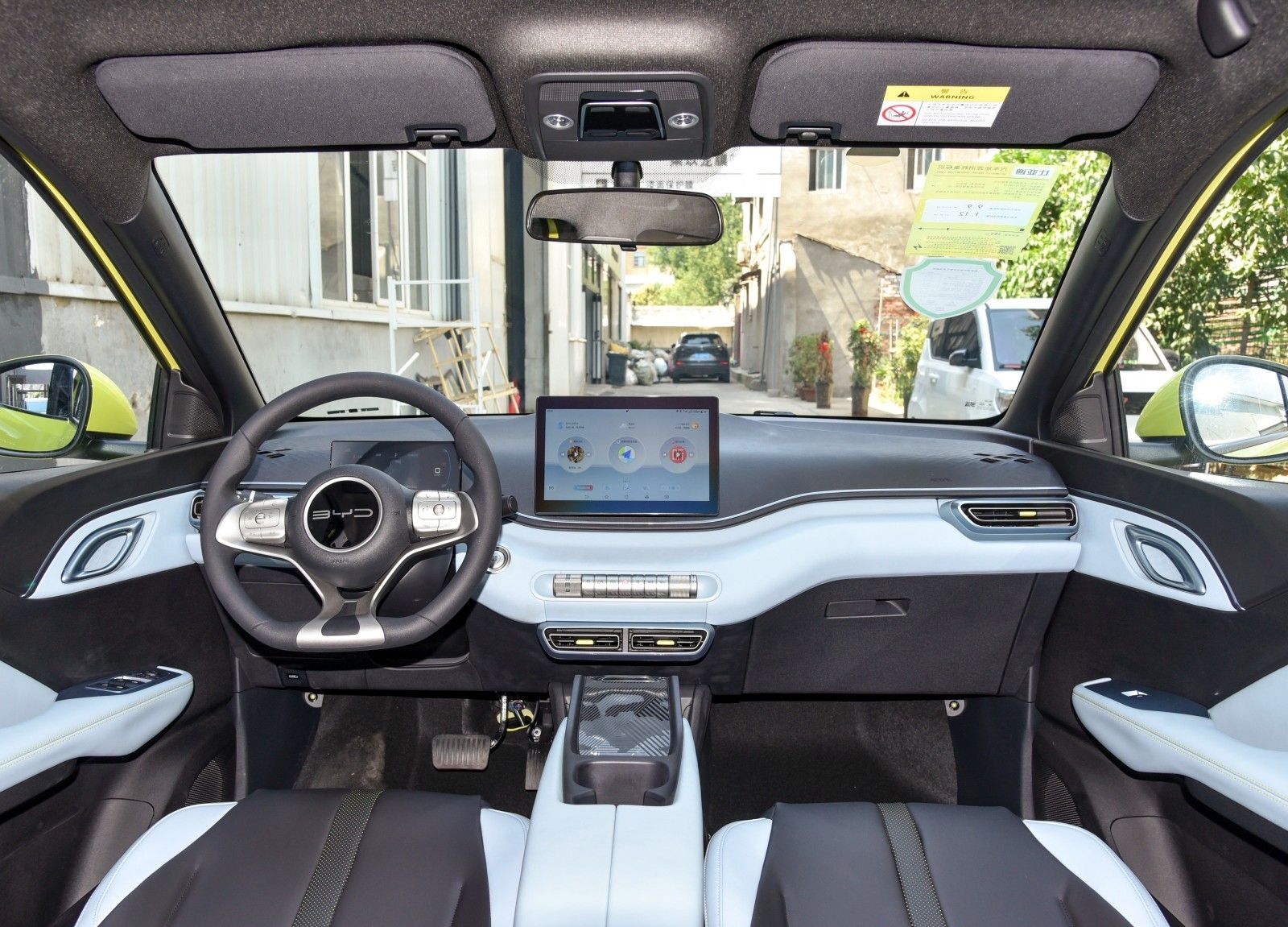
Tin mill black plate is a fundamental substrate in the production of tinplate, which is widely utilized due to its excellent properties such as resistance to corrosion, versatility, and recyclability. These are hot-rolled coils that have been cold-reduced to the proper thickness, then annealed to achieve a metallurgical structure intended for subsequent tin coating processes. The production and quality assurance processes involved in creating tin mill black plate are sophisticated, requiring state-of-the-art technology and robust quality control measures to ensure the finest results.
Modern tin mill black plate factories integrate several pivotal stages to deliver a product that consistently meets industry standards. The journey begins with slab casting, which sets the foundation for the manufacturing process. During slab casting, precise control over the composition and distribution of elements ensures that the initial material has the desired attributes. Following this, hot rolling reduces the slabs into rolls of steel, preparing them for the cold reduction process.
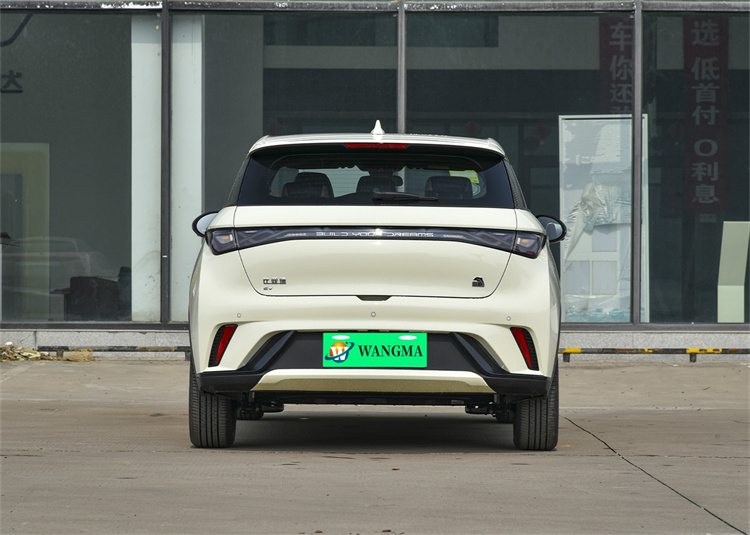
Cold reduction is a crucial phase where the thickness of the black plate is precisely controlled. Factories employ various rolling mills equipped with the latest automated technology, allowing for the production of black plates with exceptional gauge consistency and surface finish. The application of cutting-edge technology ensures that this process is efficient, reducing wastage and enhancing production speed.
After achieving the required thickness, the plates undergo a rigorous annealing process. Annealing restores the ductility of the cold-reduced steel, making it suitable for further processing and coating. In modern factories, continuous annealing furnaces are preferred for their ability to deliver uniform mechanical properties across the entire production batch, thereby assuring unrivaled product reliability and quality.
Quality assurance is another pillar that upholds the authority of proficient tin mill black plate factories. Not only must the production processes operate under strict surveillance, but comprehensive testing along the production line guarantees adherence to client specifications. Tests for surface defects, mechanical strength, and metallurgical characteristics are standard, with only batches that meet or exceed expectations moving forward in the supply chain.
tin mill black plate factories
From an operational perspective, expertise lies in efficiently managing the complexities of facility operation and maintenance. It demands highly skilled personnel familiar with intricate machinery, specialized training in quality assurance protocols, and a commitment to continuous improvement. Staying updated with advancements in metallurgical technology, factories strengthen their competitiveness and deliver innovative solutions tailored to evolving market needs.
In terms of experience, a factory's longstanding history in manufacturing black plate serves as a testament to its reliability and expertise. Factories with seasoned professionals bring depth in understanding nuanced client needs and delivering solutions that go beyond generic offerings. This gives such enterprises an edge, allowing them to cater to specific industrial requirements, provide customized service, and uphold enduring business relationships.
Further bolstering trustworthiness, sustainability plays a central role. Eco-friendly practices are incorporated into various stages of production – from recycling water used in cooling systems to minimizing the ecological impact of emissions through advanced filtration systems. Key players in this industry are increasingly leaning towards developing products with less environmental footprint, reflecting a commitment to global sustainability goals.
To capitalize on these facets, it is crucial for businesses engaging with tin mill black plate factories to align themselves with producers who demonstrate a comprehensive grasp of these attributes. Understanding a factory's capacity for innovation, stringent quality control, and commitment to sustainability could mean the difference between ordinary and exceptional product performance in the market. This approach not only places emphasis on immediate commercial gains but also fosters a sustainable, long-term partnership built on mutual growth and success.
In conclusion, the landscape of tin mill black plate manufacturing is rich with expert knowledge, technical prowess, and industry-leading practices. By prioritizing factories that embody experience, expertise, authority, and trustworthiness, stakeholders can achieve more than just product acquisition – they can set the groundwork for a robust, future-ready enterprise leveraging one of the most vital materials in modern industry.