Exploring the Dynamics of Galvanized Iron Wire Netting Manufacturing
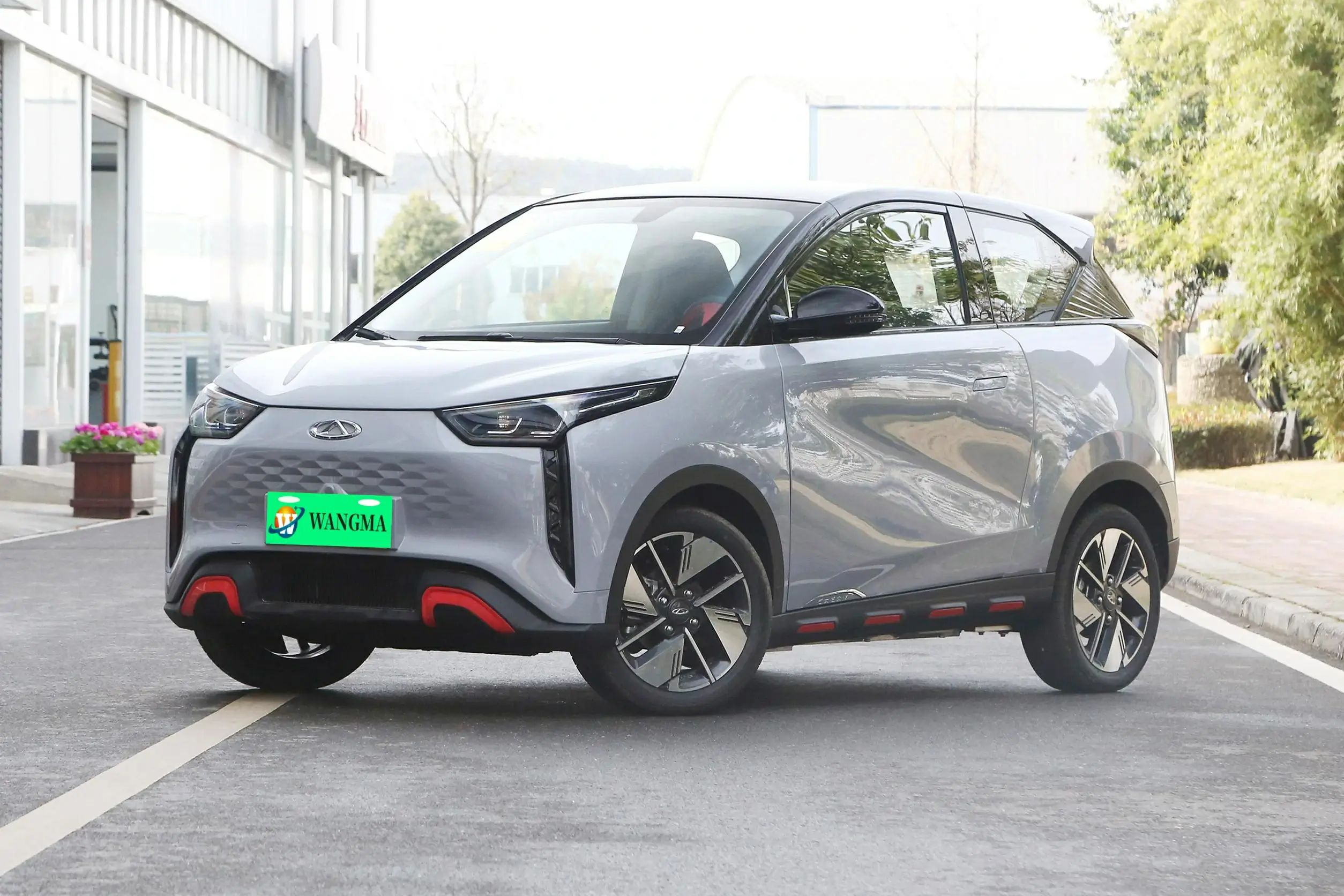
The elegance and toughness of galvanized iron wire netting have made it an indispensable resource in various industries. From agriculture to construction, the application of this robust material continues to expand, primarily due to its resistance to corrosion, versatility, and enduring lifespan. The industry of manufacturing galvanized iron wire netting stands as a testament to the convergence of traditional craftsmanship and cutting-edge technology. This article delves into the operational intricacies, technological advancements, and quality assurance practices of a top-tier galvanized iron wire netting factory.
Operational Excellence and Real-World Insights
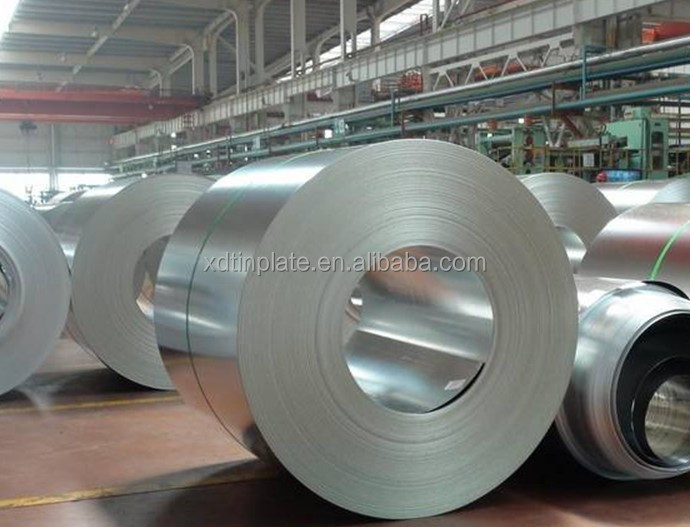
An industry leader in galvanized iron wire netting production relies heavily on operational excellence to maintain its competitive edge. Manufacturing processes often initiate with the selection of high-grade raw materials, ensuring that durability and resilience are paramount. The refinement process involves the careful calibration of wire diameters, tensile strength, and zinc coating thickness. A visit to a prominent factory reveals meticulous attention to detail, where workers streamline operations through sophisticated machinery calibrated for precision wire weaving.
Product innovation and customization have emerged as crucial differentiators among leading factories. Progressive manufacturers offer bespoke netting solutions tailored to client specifications, including variations in mesh size, wire gauge, and dimensions. By investing in advanced R&D, factories can address diverse operational challenges, providing clients with state-of-the-art products adapted to specific usage contexts such as pest control, animal enclosures, and protective barriers for structures.
Technical Expertise and Advanced Processes
Within the factory setting, technical expertise is the backbone of efficient production lines. Seasoned engineers and technicians collaborate to optimize galvanization processes — a meticulous operation that involves submerging cleaned iron wire in molten zinc at temperatures greater than 450 degrees Celsius. This creates a protective layer resistant to rust and weathering, enhancing longevity and performance.
Continuous professional development programs are quintessential, keeping technical teams at the forefront of industry innovations. Leveraging automation and digital technology, many factories streamline operations, reducing manual labor and minimizing human error. Robotic arms and automated weaving systems epitomize the modernization within these factories, ensuring consistency, accuracy, and elevated production speeds.
galvanized iron wire netting factory
Authority through Quality Assurance and Compliance
Operational authority in the wire netting sector is cemented through stringent quality assurance mechanisms and adherence to international standards. Factories implement exhaustive testing regimes, examining the physical and chemical properties of products to align with ISO certifications and national regulatory benchmarks. Destructive and non-destructive testing protocols are utilized to assess factors like tensile strength, elongation, and coating uniformity. This authoritative approach ensures that every batch of wire netting surpasses both client expectations and safety requirements.
Moreover, an ethical sourcing and environmental responsibility narrative bolsters a factory's authoritative standing. By employing eco-friendly galvanization methods and recycling zinc materials, factories uphold sustainability principles. This not only enhances brand image but also aligns with growing consumer demand for environmentally conscientious products.
Trustworthiness through Customer Engagement and Transparency
Trustworthiness transcends mere product reliability, encompassing transparent communication and proactive customer engagement. Reputable factories establish enduring partnerships with clients, offering comprehensive consultation services and after-sales support. By providing insights into maintenance best practices and longevity optimization, manufacturers demonstrate an unwavering commitment to client satisfaction and trust.
Digital platforms play an instrumental role in fostering trust. A well-designed website with detailed product information, client testimonials, and case studies serves as an informative resource, guiding potential clients in their decision-making processes. Through transparent data-sharing and customer-centric narratives, factories cultivate a trustworthy digital presence that strengthens their market positioning.
In summary, the galvanized iron wire netting sector is a vivid illustration of how traditional industries are evolving through innovation, expertise, and an unyielding commitment to quality. As demand continues to escalate across various domains, factories that excel in operational efficiency, technical prowess, and customer engagement will undoubtedly lead the charge towards a more sustainable and secure future.