Galvanized iron has found its niche in a host of industrial applications, prominently among them being gas factories. With its combination of durability, cost-effectiveness, and resistance to corrosion, galvanized iron presents an ideal material choice for enhancing both functionality and safety standards in gas production facilities.

In the challenging environment of a gas factory, where materials are constantly subjected to corrosive elements and high pressures, choosing the right construction materials is crucial. Galvanized iron's application in these settings offers a multitude of benefits that go beyond mere structural integrity. This article delves into why galvanized iron is a staple in gas factories and examines the comprehensive impact it has on operations.
From a practical standpoint, galvanized iron stands out primarily for its corrosion resistance. This quality stems from a protective layer of zinc applied during the galvanization process. This coating acts as a shield, preventing moisture and harsh chemicals commonly found in gas factory environments from coming into direct contact with the iron. This extended lifespan reduces frequent maintenance and replacement costs, offering long-term financial savings.
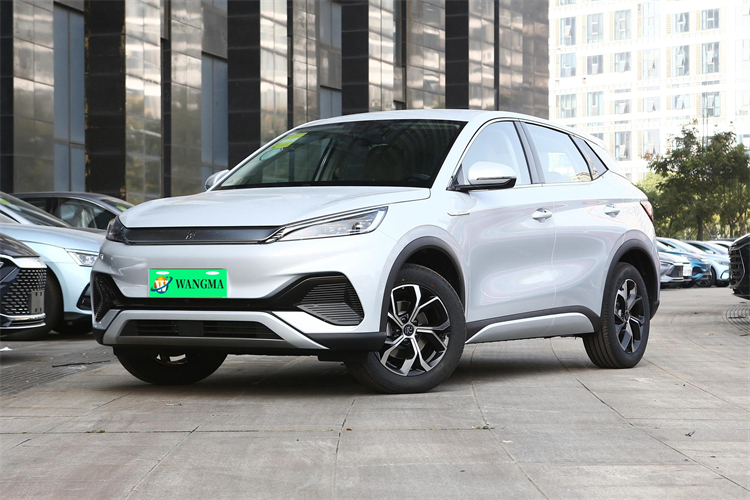
Moreover, the robustness of galvanized iron ensures it can withstand mechanical strain better than many alternative materials. In gas production facilities, where components face continuous pressure and stress, having reliable infrastructure is paramount. Equipment failure or breakdowns can lead to not only costly repairs but also potentially hazardous situations. Galvanized iron’s strength offers peace of mind by ensuring that structural components maintain their integrity over time.
A critical aspect of galvanized iron's efficacy lies in its adaptability. Gas factories often require custom solutions to fit unique operational needs. Galvanized iron can be easily fabricated into various shapes and sizes, allowing for bespoke solutions tailored to specific factory layouts and design requirements. This flexibility is invaluable in optimizing space and improving the efficiency of gas processing operations.
Galvanized iron also supports environmental sustainability efforts, a significant consideration for modern industries increasingly leaning towards greener practices. The galvanization process is sustainable, with the materials used—iron and zinc—being recyclable. This means that implementing galvanized iron is not only a choice for durability and cost-effectiveness but also contributes to reducing the carbon footprint of factory operations.
galvanized iron for gas factory
The use of galvanized iron in gas factories is not only about meeting immediate operational needs but also ensuring compliance with stringent industry standards. Regulatory bodies often impose rigorous requirements on materials used within gas production facilities, aiming to ensure both safety and environmental compliance. Galvanized iron meets these standards, providing a reliable and industry-applicable solution that aligns with global safety regulations.
Case studies across several prominent gas factories worldwide have demonstrated the effectiveness of galvanized iron in field applications. These instances highlight significant reductions in both maintenance downtime and incidences of material failure, reaffirming the material's reliability and endurance. Furthermore, positive feedback from engineers and operations managers positions galvanized iron as a go-to material choice, underscoring its established reputation in the industry.
When discussing the benefits of galvanized iron, it is also essential to recognize the role of trusted suppliers and proper installation. Collaborating with experienced providers ensures that the galvanized iron supplied meets the highest quality standards and is suitable for specific applications within gas factories. Proper installation ensures that these materials perform optimally, minimizing the potential for unforeseen issues.
Lastly, ongoing research and development in galvanization technologies promise to enhance the capabilities and features of galvanized iron even further. Innovations in coating techniques and materials science are poised to increase the lifespan and functionality of galvanized products, keeping them at the forefront of industrial material solutions.
In conclusion,
galvanized iron proves to be more than just a structural material for gas factories. It is a comprehensive solution that addresses key operational challenges, offering enhanced durability, flexibility, and compliance with industry standards. By choosing galvanized iron, gas factories can not only optimize their current operations but also pave the way for sustainable and efficient future practices. As industries evolve, galvanized iron stands ready to meet the demands of modern gas production, maintaining its standing as a cornerstone material in the sector.