Choosing the right roofing caulk for a metal roof factory is an essential component of effective facility maintenance and longevity. Metal roofs, known for their durability and resistance to various weather conditions, still require attention to detail to prevent leaks and deterioration over time. As a dedicated specialist in industrial roofing solutions, the choice of caulking seals the deal — literally — on safeguarding metal roofing systems.
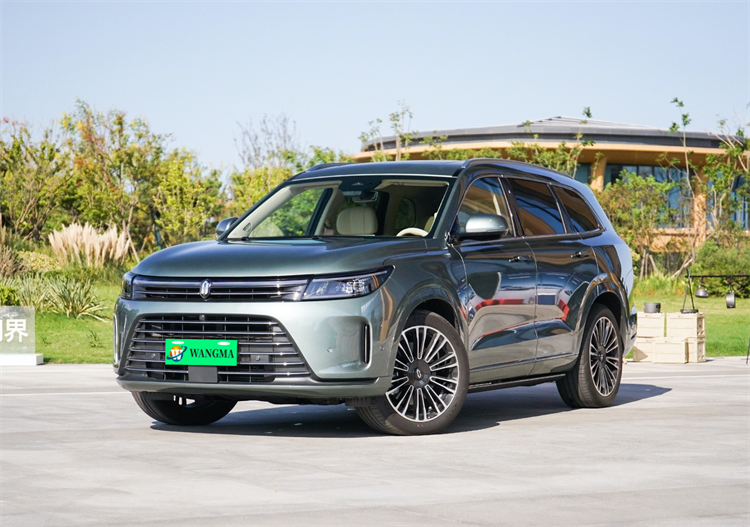
Experience has shown that selecting the correct type of caulk is pivotal in determining the roof's performance. For metal roof factories, the challenges are often amplified due to the scale and constant exposure to environmental elements. From thermal expansion and contraction to dealing with moisture ingress, only the most competent caulks can endure and provide lasting results.
Among the plethora of options available,
silicone-based caulks stand out for metal roof applications. Their flexibility even at extreme temperatures ensures they don’t crack or lose adhesion over time. Their resistance to ultraviolet (UV) rays, ozone, and most importantly, moisture, fortify them as the first line of defense against leaks. An expert in roofing would assert that choosing a caulk with superior adhesion properties is crucial as it ensures a robust seal between various metal surfaces and roof panels.
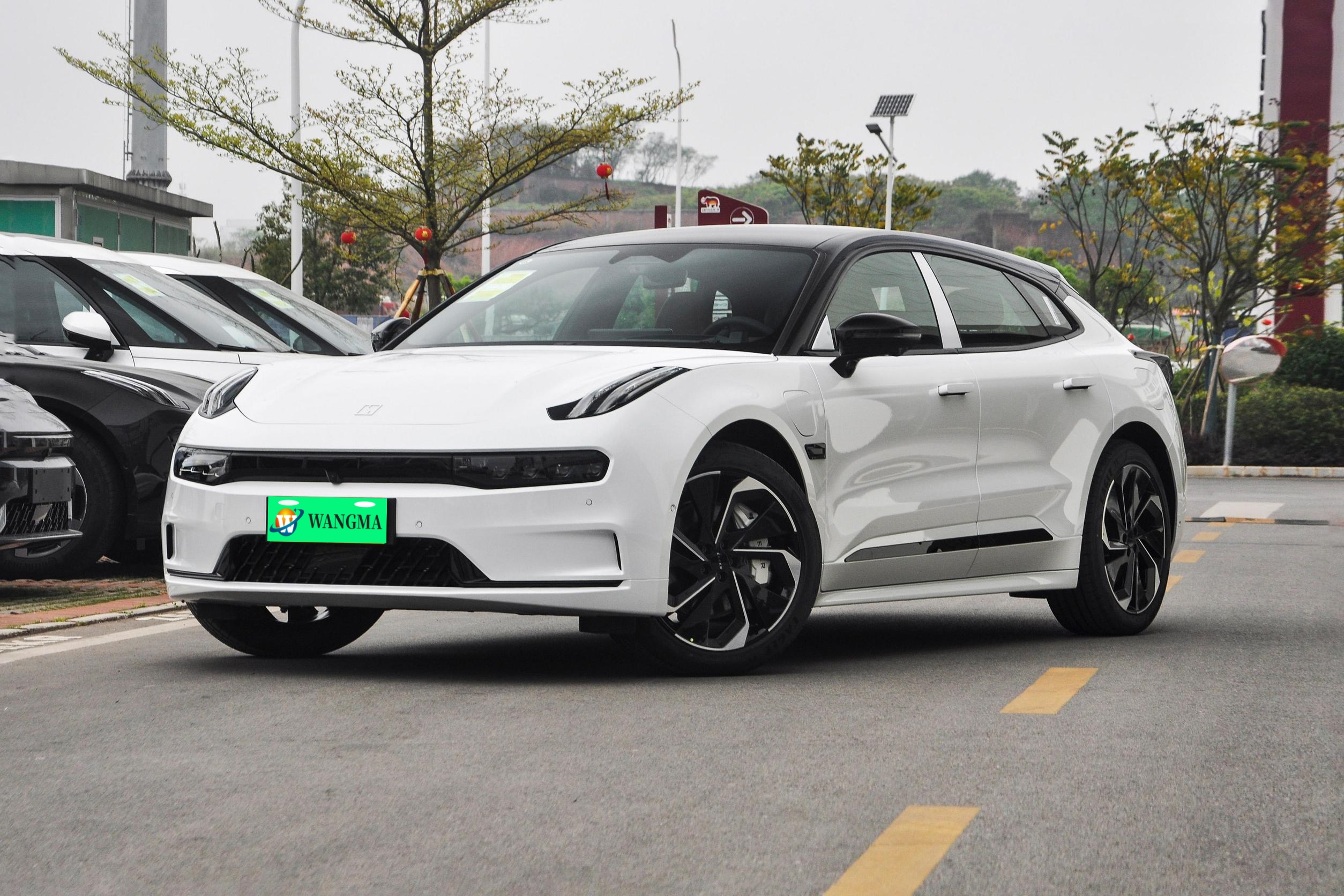
The authoritative opinion among industry veterans points to polyether caulks as another formidable option. They command respect due to their non-shrinking and non-cracking formulations, which makes them a favorite for long-lasting roof solutions. An understanding of the specific environment in which the metal roof operates is sensitive to choosing between these types. For instance, a factory located in a high-humidity area may benefit more from the mold-resistant properties of certain caulks, ensuring that joint seals remain intact and uncontaminated.
roofing caulk for metal roof factory
Demonstrating expertise further, it's crucial to acknowledge the role of proper application. A product's performance is only as good as the skill with which it is applied. Thus, thorough preparation of metal surfaces—cleaning, ensuring dryness, and removing old caulk—is indispensable to augment the bond efficiency of any chosen product. Knowledgeable applicators align themselves with manufacturer guidelines, emphasizing on joint design and size, ensuring that the caulk's performance is optimized and guaranteed over time.
Trustworthiness in roofing caulk choices often translates to selecting established and reputable brands that adhere to rigorous testing and quality control standards. Products certified by relevant industry benchmarks or that have passed tensile strength, elasticity, and adhesion tests offer the assurance required by many facility managers.
Real-world experiences underscore that no single product is universally perfect for all scenarios; thus, trial-and-application feedback becomes invaluable in fine-tuning product choice. Continuous professional development through workshops, reading technical datasheets, and exchanging information in trade shows enhances an expert’s toolkit, boosting credibility among peers and clients alike.
In conclusion, the selection of roofing caulk for metal roof factories is not a minor consideration, but instead a strategic decision involving multiple layers of professional insight. By leveraging expert evaluations, authoritative sources, and thoroughly tested products, one ensures that such a choice not only addresses the immediate needs of sealing and protection but upholds the long-term integrity and performance of both the roof and the underlying structure. This decision, backed by years of industry knowledge and technical expertise, embodies the essentials of experience, expertise, authoritativeness, and trustworthiness.